top of page


Welcome to
Scan Tool & Mold Inc.
From Pellet to Product
ISO Class 8 Clean Room Molding
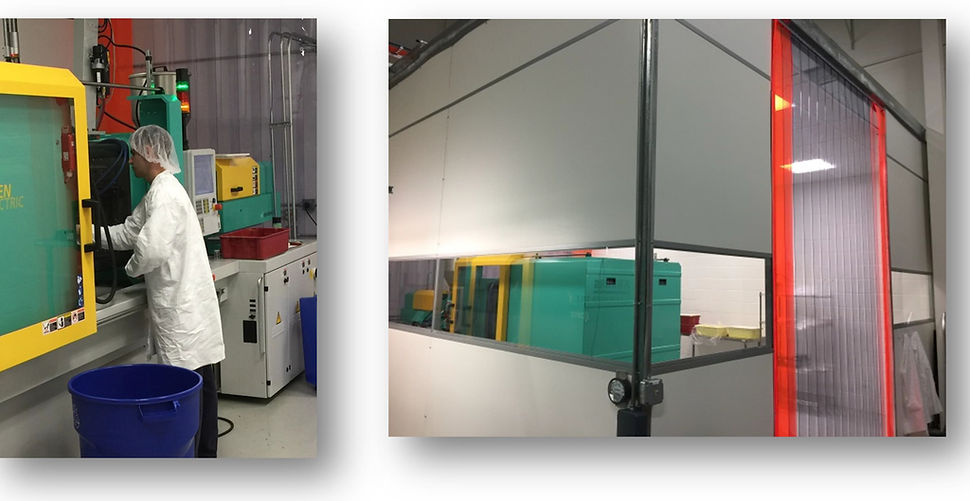
Why Mold Parts in a Clean Room?
In industries where precision and contamination control are critical, molding parts in a clean room environment is essential. Clean room molding ensures the highest levels of quality, sterility, and consistency, making it an indispensable practice in sectors such as medical devices, pharmaceuticals, electronics, and high-end automotive manufacturing. Here’s why investing in clean room molding is a strategic advantage:
-
Contamination Control - Clean rooms are meticulously controlled environments designed to minimize airborne contaminants such as dust, microbes, and other particulates. This level of control is crucial for industries where even the smallest impurity can compromise product integrity. For example, in medical device manufacturing, contamination can lead to device failure or pose serious health risks to patient
-
Regulatory Compliance - Many industries must adhere to stringent regulatory standards, such as ISO 13485 for medical devices, ISO 14644 for clean rooms, and FDA requirements for pharmaceutical manufacturing. Clean room molding helps companies meet these strict guidelines by providing a controlled and validated environment that ensures consistent compliance.
-
Superior Product Quality and Consistency - By eliminating environmental variables such as airborne particles and temperature fluctuations, clean room molding produces high-precision parts with superior surface finishes and dimensional accuracy. This consistency is especially critical in industries like aerospace and microelectronics, where precision is non-negotiable.
-
Reduction of Defects and Waste - Contamination during molding can lead to defects, rework, and costly material waste. By molding in a clean room, manufacturers significantly reduce the risk of contamination-related defects, thereby improving production efficiency and reducing overall costs.
bottom of page